Australian scientists have demonstrated a new type of 3D-printed titanium structure that is ultra-strength, lightweight and has increased corrosion and heat resistance. Soon, their material, which takes relatively little time and money to produce, may find application in the aviation and space industries, which currently use expensive magnesium-lithium alloys.
Metamaterials are artificial materials created in the laboratory, including those printed on a 3D printer. They can consist of one or several conventional materials. Their main difference from ordinary ones is the presence of properties planned by the creators that are not found in the latter.
Over the past 20 years, engineers have created many metamaterials with metallic inclusions in the form of a lattice – from titanium, aluminum alloys, nickel-based alloys, and stainless steel. Although they were better than most structural materials, only a few were more effective than the same magnesium alloys, widely used today in aircraft and rocketry due to their low density, high specific strength, and vibration-insulating properties.
Therefore, scientists have long been trying to create “raw materials” that could work in difficult conditions: be ultra-strong and withstand extreme temperatures and pressures.
Australian researchers at the Royal Melbourne University of Technology have created a new metamaterial from titanium alloy Ti-6Al-4V (an alloy of titanium itself, six percent aluminum, and four percent vanadium) that is 50 percent stronger than the strongest commercial magnesium alloy WE54 of similar density (1, 85 grams per cubic centimeter). Ti-6Al-4V is one of the most commonly used titanium alloys, and it is used where low density and high corrosion resistance are required in the aerospace industry. The results of the work were published in the journal Advanced Materials.
Nature has become a source of inspiration for scientists. They studied plants with strong stems and hollow tubular structures that combine strength and lightness, such as water lilies ( Victoria boliviana ) and corals ( Tubipora musica ). The researchers then tried to replicate this structure in practice. To do this, they used 3D printing.
“Many scientists have tried for decades to recreate these natural hollow “cellular structures” in metal but have continually failed. One of the main reasons this did not work was the resulting stress at the connection points of the internal sections of the hollow struts, which led to the destruction of the structures. Ideally, the stress should be evenly distributed throughout the material,” explained Ma Qian, leader of the study.
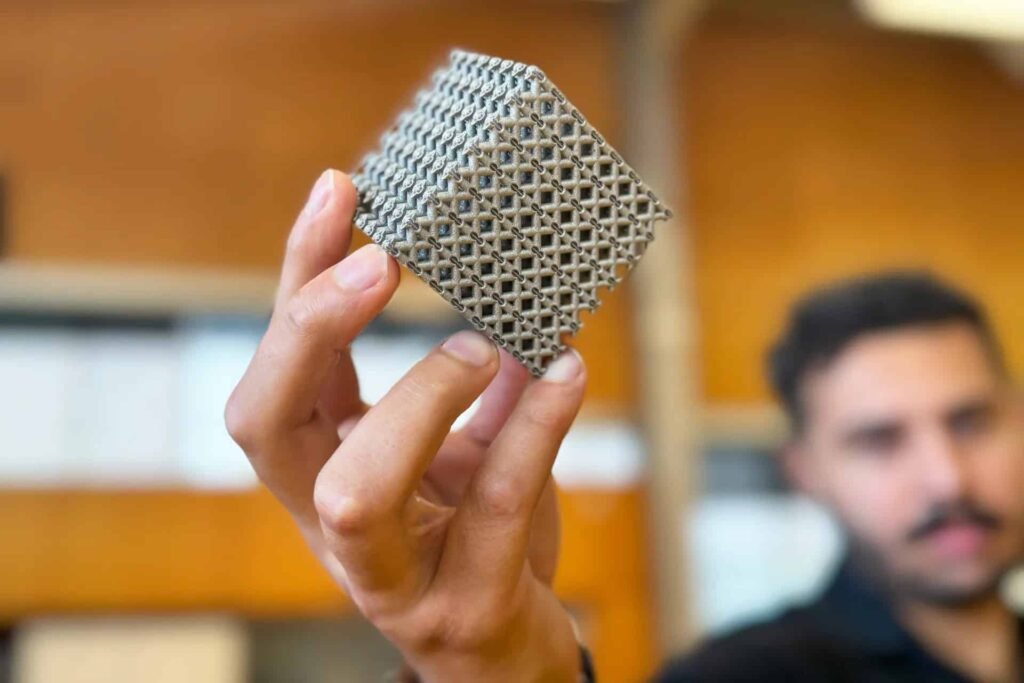
To reduce the high-stress level generated at the connection points of the “laboratory” tube grid, Qian and his colleagues strengthened it by placing a second grid on top, adding a thin cross-shaped cut through the pipes and connections. This made it possible to distribute the load evenly during compression.
To manufacture such a structure, specialists used a 3D printing method called laser melting of metal in a pre-formed layer ( Laser Beam Powder Bed Fusion ). This is one of the most proven technologies for printing metal products, and it uses a powerful laser beam to melt metal powder compositions.
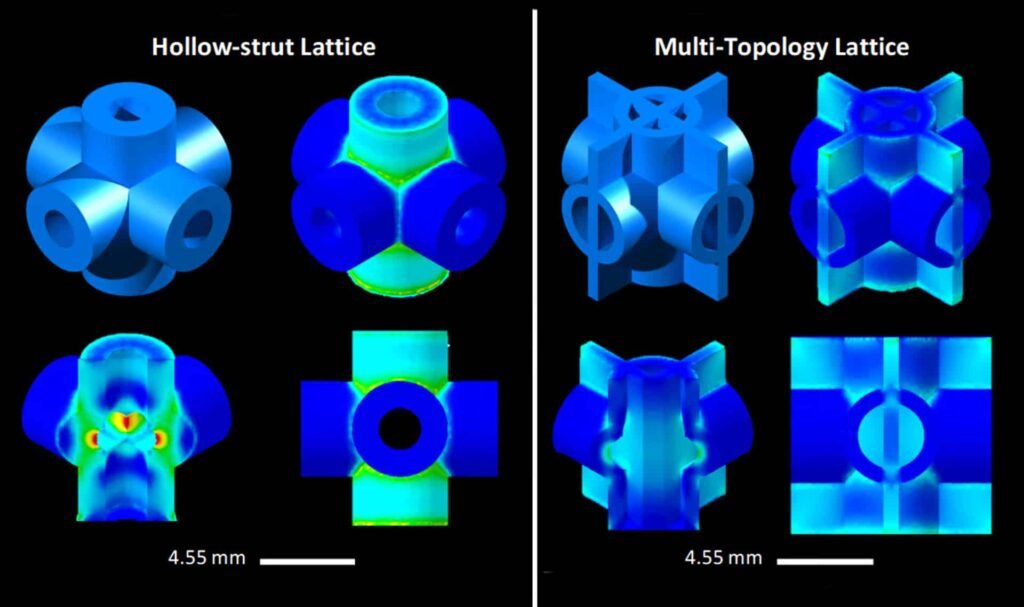
The scientists tested their metamaterial in the laboratory under various challenging conditions. The printed structure, a titanium cube, was 50 percent stronger than WE54 magnesium-lithium alloy, considered the strongest commercial alloy in the aviation and space industries.
Depending on the available printers, the metamaterial samples can easily change in size from a few millimeters to several meters. They can withstand (with this composition) heating up to 350 degrees Celsius or up to 600 degrees if more heat-resistant titanium alloys are used.
According to the study authors, shortly, their material will be suitable for the manufacture of parts of aircraft and rocketry, unmanned fire systems, as well as for the creation of bone implants in medicine, where a complex, partially empty mold can be filled over time with regrown bone cells.